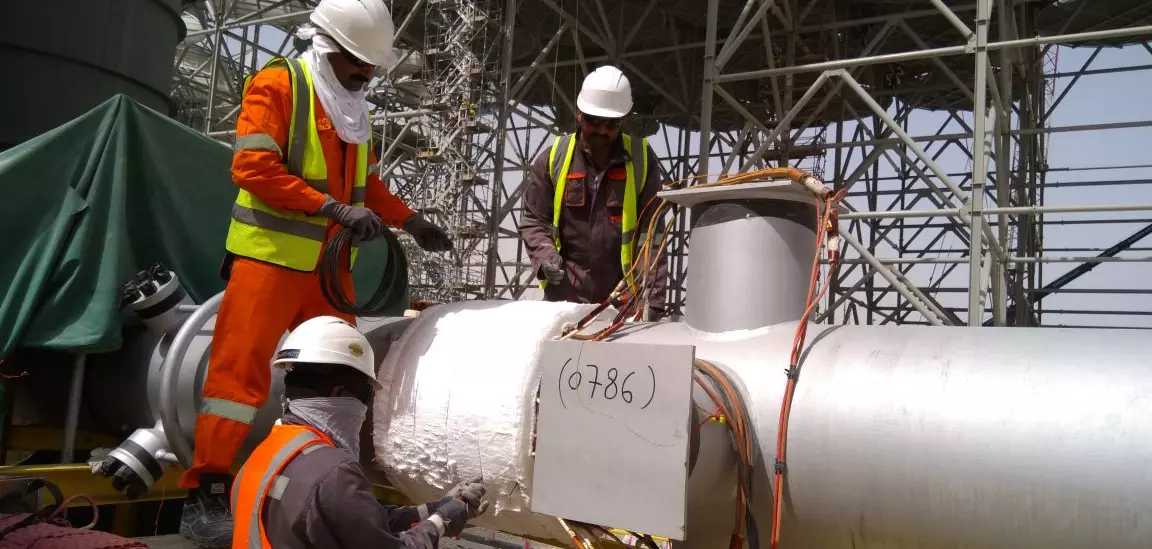
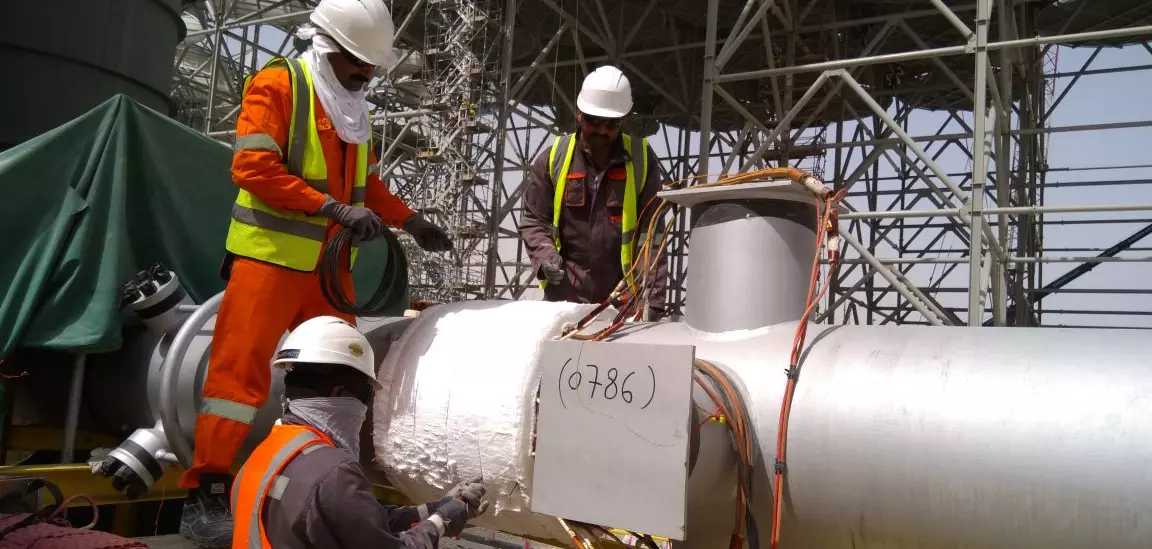
Heat Treatment Services
GR specializes in performing heat treatment for the steel and metal fabrication industries including the construction of pressure vessels, pressure piping, storage tanks, buildings, bridges, offshore platforms, power plants, oil and gas refineries, and petrochemical plants.
There is often a mandatory requirement for heat treatment due to compliance with welding codes and specifications on certain materials including but not limited to carbon steels, stainless /high alloy steels and work hardened steels. There may also be heat treatment requirements based on the wall thickness of the parts being welded together. Heat Treatment reduces or redistributes the residual stress introduced by the welding process with a technique that involves heating, soaking and cooling the weldment/machined surface to controlled temperatures.
Pre-Heating
Thermal stresses are set up as a molten weld cools. Cracking can occur during and after welding. Pre Heating reduces the temperature differentials between the weld metal and the parent metal, thus minimizing the tendency to crack.Post Weld Heat Treatment (PWHT)
PWHT is carried out by electrical resistant method or by (furnace firing or internal firing) with high velocity fuel burners. There are three main benefits, stress relaxation, tempering and hydrogen removal. The first two benefits are generally the reason for the heating operation, with hydrogen removal being considered as a bonus.Normalizing
Normalizing / Annealing heat treatment is to improve the mechanical properties of steel, tensile strength and impact value are improved leading to better resistance to brittle fracture. For instance, with mild steel, the temperature would be approximately 900ºC (1650F) that is 50ºC above the upper critical point.Solution Heat Treatment
Certain types of austenitic stainless steel undergo structural changes in the range of 500º to 800ºC which are detrimental to their corrosion resistance properties. Weld decay occurs. One method of obtaining immunity from decay is by raising the material to 1000 – 1150ºC followed by rapid cooling.Refractory Dry Out
All types of furnaces have a kind of refractory insulating installed in it and this need to be dried out the method in heating the surface gradually until it reaches the recommended manufacturer procedure.Contact
India
+91 44 6666 1000 ~ 1099
Bahrain
+973 17 811 757
UAE
+971-26224033
Qatar
+974 4481 6986
Azerbaijan
+99412 441 58 82
USA
+1 972 961 4814
Turkmenistan
+993 12 483303
Iraq
+964 7508689553
Case Study
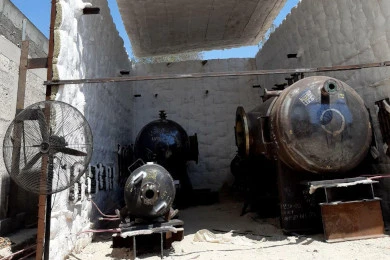